正确看待国产民用碳纤维的现状
国产碳纤维的技术和水平在近10年的发展态势喜人,但是我们不能盲目自大,只有知己知彼,才能在碳纤维战场拔得头筹。碳纤维的核心技术一直掌握在日本和美国手里,想要追赶并超越他们,越要的不仅是时间,更是巨量的投入。
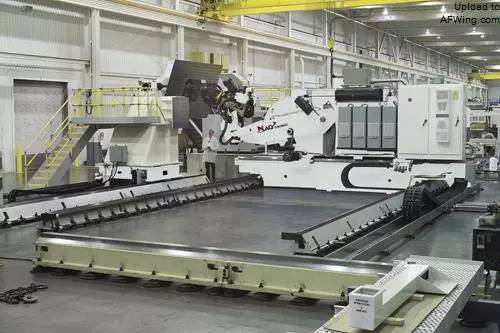
中复神鹰碳纤维航空应用项目在上海开工
8月18日,中复神鹰“碳纤维航空应用研发及制造”项目在上海临港新片区大飞机产业园正式开工。与该项目配套的研发中心同步启动建设,主要进行航空树脂、航空用碳纤维复合材料中间制品的研发,计划2022年将陆续开发新产品,并开展航空应用评价认证工作。
不仅仅是中复神鹰上海碳纤维基地,还有吉林碳谷,新疆碳纤维工业园等多个大型碳纤维项目上马,这些都是我们在碳纤维产业中走出的坚实的步伐。
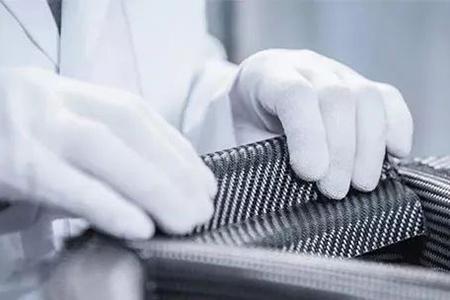
正确看待国产民用碳纤维现状
得益于前面10年的大力发展,我国在军用小丝束碳纤维上的进度巨大,已经可以满足国防需求,但是这并不是终点,反而只是个起点,因为大丝束民用碳纤维应用的市场规模更大,对于碳纤维制备来说技术难度更大,只有将小丝束军用碳纤维和大丝束民用碳纤维技术都牢牢的掌握在自己手里,才能真正的赶超日美。
先借用咱们中国材料大师师昌绪老先生在2010年的评论:目前中国的碳纤维复合材料的应用水平,大约处于西方发达国家1980年代的水平。即便现在已经是2021年了,但是这中间的差距并没有被缩小很多,尤其是大丝束民用碳纤维方面,为什么差距还是如此巨大?我们来分析分析原因。
1、政策层面:战略军用小丝束产品,得益于两代“核心”领导的重视,T300军用碳纤维的完全国产化,使得次承力结构军用构件有较快的发展。而民用大丝束领域的政策扶持相对滞后许多。实际上,国家当年资源人力都有限,为了救急,集中精力搞军用小丝束,是完全合理的。但是,从长远来看,通用、民用产品的市场空间更大,是碳纤维行业持久发展、持续创新的厚土沉基。在军品已经打开突破口,经济发展、国力增强的今天,不要说大丝束,即便是小丝束产品,也应当更多的从市场和民用角度,拓宽其行业基础,以军带民、以民养军、分苗嫁接、开枝散叶,形成军用技术和民用产业的良性互动。
2、PAN原丝和碳纤维生产层面:国内十数家碳纤维生产厂家,群雄并起,看似热闹,实际上有很大一部分并没有掌握核心技术。要么是关键设备、关键材料需要进口,要么是工艺参数和质量控制没有吃透。甚至,很多企业到现在,PAN原丝生产还要高价进口东丽公司的DMSO溶剂,属于照猫画虎形的“自主生产”。多数厂家的产品质量批次差异性较大,缠结、断丝时有发生,合格的PAN原丝生产量不过100吨/年,达不到基本规模经济水平。产业布局和关键技术的把握,都有很大的提升空间。
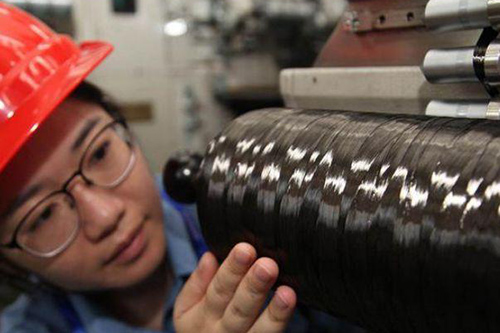
3、碳纤维复材生产层面:在预浸料自动铺叠技术和整体成型工艺,已经成为发达国家成熟制造技术,但对于中国航空航天碳纤维复合材料领域,依然是工业化生产中最大的一块短板,甚至空白。即便有了引进设备,我们对复材的物理性质,力学性能研究不透,对加工参数掌握不足,知其然不知其所以然,直接用国外的软件设计复材方案,导致CFRP复材的产量低、价格高、质量不稳定和创新能力低下。军用部件不计成本,也就罢了,而对商业化批量生产和应用,这就是一个重大的阻碍,很多厂家为此畏难而退,裹足不前,干脆直接用已经摸透的金属材料做更有把握和更经济。
4、碳纤维设计思想层面:航空航天器的设计,需要结合复材性能特性,加强整体设计的思想,而不是简单的替换原金属部件。举一个简单的例子,国内某型军机的平尾改用CFRP复材后,确实轻了不少,但却因此改变了全机力矩平衡,需要通过配重进行调整,结果整机减重效果并不理想。当然,逐项替代也是一种有效的验证步骤,但有一种理念需要强调:局部优化不代表整体优化。在复合材料应用愈加广泛的今天,顶层设计,全局优化,才能最大化的发挥复材的最大功能效用和经济效用。
看到这里,可能很多人会有些沮丧,毕竟追赶了10年,我国的碳纤维水平距离日美还有至少20年的差距,但是我们的发展速度是日美望尘莫及的。虽然我们的起点比较低,但是我们有激情、有资金、有人员、有目标、有勇气、有行动,那我们可以用下一个10年,甚至好几个10年,来完成碳纤维技术水平的赶超。
文章转载说明:本文由金洋6新材料整理编辑发布,版权所有,未经允许不得转载。
上一篇:正确看待国产民用碳纤维的现状